Health and safety audits are essential to building an organization’s safe working environment and culture. The importance of a health and safety audit is an integral part of any management system. This blog post will help guide you through the entire process, explaining:
What is a health and safety audit?
What is the importance of a health and safety audit for the business?
What is the reason for conducting health and safety inspections?
Who performs health and safety audits?
What factors are critical to health and safety inspection?
How often should health and safety audits take place?
What are the standards for health and safety audits?
What steps are involved in health and safety audits?
What is the importance of reviewing after health and safety audits?
Let’s begin!
What is a health and safety audit?
Health and safety audits form an integral part of the health and safety management system to ensure that the workplace has a safe and healthy environment, free from any risk or hazard, assuring employee safety while working.
It is a systematic, periodic, and recorded evaluation of the health and safety within an organization, whether the system of the license is compliant with the standards set by the industry and regulatory bodies and independent health and safety auditor.
What is the importance of a health and safety audit for the business?
A health and safety audit assesses the health and safety conditions prevailing within an organization to ensure employee safety. The goal is to evaluate workplace policies, procedures, and processes and suggest areas of improvement.
A health and safety assessment answers the following questions:
- Is your business compliant with regular laws and regulations?
- Are the policies comprehensible and well-communicated through the hierarchies?
- Is process documentation easy to follow?
- Do you have a safety system in place that ensures employee safety?
- Do you encourage involving your workforce in the organizational safety culture?
A well-implemented health and safety audit provides the following benefits:
Compliance:
A well-executed health and safety audit will ensure that your organization complies with updated rules and regulations and best industry practices. This significantly minimizes the risk of persecution in case any incident occurs.
Cost- savings:
Since a health and safety audit helps you identify the problem area, it also saves money that would have been otherwise spent in case of an accident. Furthermore, implementing the recommendations and corrective action suggested by the auditor helps minimize the number of mishappenings.
Safety:
This is the primary goal of conducting an organization’s health and safety audit. Since audits set up recommendations and corrective action for improved communication of procedures, the possibility of accidents and incidents decreases significantly.
What is the reason for conducting health and safety inspections?
Health and safety audits are conducted for several reasons. Still, most importantly, it is done to identify any potential hazard that may result in an accident, make recommendations and take corrective actions to make the workplace a safe environment.
Who performs health and safety audits?
While health and safety audits can be performed by government bodies, the external audit team, and internal leadership teams, there are three types of health and safety inspection that different professionals perform:
- Safety Survey: They are performed by health and safety specialists who review beyond the general survey and into dangerous areas and what goes within the operation.
- Incident Inspection: This is done to identify the root cause of an incident that has recently happened.
- Walkthroughs or Tours: These are general inspections performed by the leadership team to ensure that there are no hazards in the workplace and that it is a safe work environment.
What factors are critical to health and safety inspection?
Health and safety audits should be conducted in compliance with the best industry practices. Here are some crucial elements that are critical to health and safety audits:
Competent Auditors:
A health and safety audit is as good as the professional conducting it. This is why the auditor you designate this task to must have extensive knowledge and demonstrable experience. You can outsource the consultant to conduct the process or create a team of in-house professionals who are sound in safety standards. While hiring in-house professionals, ensure they are well educated on the regulatory laws, OSHA, and other standards. Furthermore, they should be trained in violation and hazard identification.
Consistency:
The standard practice followed by most organizations worldwide is to conduct health and safety audits annually. While this is helpful, it results in a ramping-up atmosphere where the managers and supervisors would be seen running here and there to ensure compliance in every document and process right before the audit. A better option would be to schedule a health and safety audit over 3-6 months and conduct a comprehensive safety audit annually. This consistency will ensure that your organization complies with industry standards around the clock.
Preparation in Advance:
Auditing can be a taxing experience which is why it is crucial that those who are auditing and those who are being audited have prior experience beforehand and have made the necessary repairs. All the managers and supervisors affected by the audit should be informed at least one week before so that they can gather all the relevant records and documents for checking.
After determining the scope of the audit, it would be helpful for the organization to give a refresher to the designated people on legal and standard requirements. The safety audit team should keep an eye on all the audits that have happened in the past, along with the recommendations for corrective actions ensuring that the legal, local, state and federal requirements have been met.
Recordkeeping:
To identify the potential problem areas, the organization needs to create detailed records they can consult while auditing. These reports help the auditors better scrutinize the problem areas. Furthermore, it is essential to have a safety checklist that the auditor can go back to and ask questions to the people in the operational field to gather complete information about the place and any potential hazards lurking around it.
Data Analysis:
Once all the documents, written programs, procedures, work practices, and the area is audited, it is time to gather all the report and conduct a data analysis to identify the problem area. The data analysis can help check whether all the recommendations, audit comments, and corrective actions have been considered and implemented and whether or not there is documented proof of compliance.
How often should health and safety audits take place?
While health and safety audits should be conducted annually, the actual frequency depends on certain factors, like the level of risk and the nature of hazards that are being identified. More prominent organizations tend to conduct health and safety audits every three or six months to ensure a safer workplace that is compliant with the regulatory bodies.
Some organizations are forced to conduct health and safety audits due to internal policies, direction from stakeholders, or as a requirement from regulatory bodies. If necessary, unscheduled audits can also be conducted to ensure that the workplace is safe for employees. These unscheduled audits will uncover the problem areas that otherwise get overlooked. It is important to note that significant changes in the business’s infrastructure, adoption of a new technology, laws, regulation, working conditions, and other factors can trigger safety audits.
What are the standards for health and safety audits?
While preparing for health and safety audits, an organization should keep international, regional, and countrywide health standards in mind. ISO 45001 is the standard for health and safety at work, developed by national and internal standard committees. These standards help in gauging the different levels of risks which might be overlooked, like restricted spaces, workers managing work at height, guidelines surrounding exposure to chemical hazards, electrical work, psychological, ergonomics, and physical risks prevailing in the workplace.
Employee participation has become an essential factor in the health and safety audit. An updated version of the International Standard for Health and Safety management focuses on including employees in health and safety decisions. This has resulted in an increased number of organizations collaborating with employees and contractors from different operational departments, including them in the health and safety programs and committees.
What steps are involved in health and safety audits?
There are three steps involved in ensuring the success of health and safety audits:
Prepare for the Audit:
- Make it a point to inform all the managers and supervisors about the audits so that all the documents are readily available for the audit.
- If you have conducted suits in the past, review them and check for corrective action, legal requirements, and training requirements that need to be audited or updated.
- Set a timeline for the audit after determining the scope of the audit.
Conduct your research:
If you plan to do a team-based auditing, inform all the managers and provide them with the assignments after defining the area so that all the necessary information can be gathered.
You can define the following areas:
- Employee Comprehension
- A written program review
- Program implementation and management
- Monitoring and reviewing of records and documents
- Equipment and material safety
Review the discovery:
Create a concise report by combining all the data obtained from the audit. Make sure that it answers the following questions:
- Are the industry practices and regulatory terms met?
- Is the proof of compliance documented?
- Are the requirement of the program met?
- Are the employees being trained properly and effectively?
Once all this is done, it is time to make recommendations based on the data finding and take corrective actions. Your corrective actions should involve setting priorities based on the hazards and including the managers and supervisors to ensure that these actions are being implemented.
What is the importance of reviewing after health and safety audits?
Monitoring and reviewing processes are essential to a health and safety audit. This helps develop an action plan by correctly assessing the control and risk involved in operating a workplace. Health and safety management systems work on a plan called PDCA system which is Plan, Do, Check, and Audit. Monitoring and reviewing fall under Check and Act system, which includes the requirements from ISO 451 and some recommendations that have been made within HS(G)65. Organizations need to:
- Measure their performance
- Ensure that the plans have been implemented
- Keep a check on how well the risk is being controlled
- Probe any mishappening or accidents, if there had been any
After reviewing the performance, it is vital to go through the plan and update it as the demands change. Businesses should also learn from the experience, errors, and any accidents, lessons which should be included in the audit and inspection reports.
When organizations are proactive in ensuring that the employees have a healthy and safe environment to work in, they mitigate and can better control risks that cannot only be hazardous but also taint the reputation of the organization. Business leaders must create such programs and promote participation by educating the workforce. This will help align the health and safety program with the vision and goal of the business.
How VisiumKMS Promotes Safety In The Workplace
VisiumKMS addresses all regulatory standards of Process Safety Management (PSM), such as the U.S. Occupational Safety and Health Standard 29 CFR 1910.119, ensuring all 14 elements of a process safety management plan. Our process safety management software helps you maintain all your process safety information in one system, using best-in-class, standardized workflows developed by industry experts!
We commit to staying ahead of the curve; to help our customers keep ahead of the business and operational pressures, regulations, and global or local challenges they face. To discuss your needs with one of our experts, schedule a call with us here.
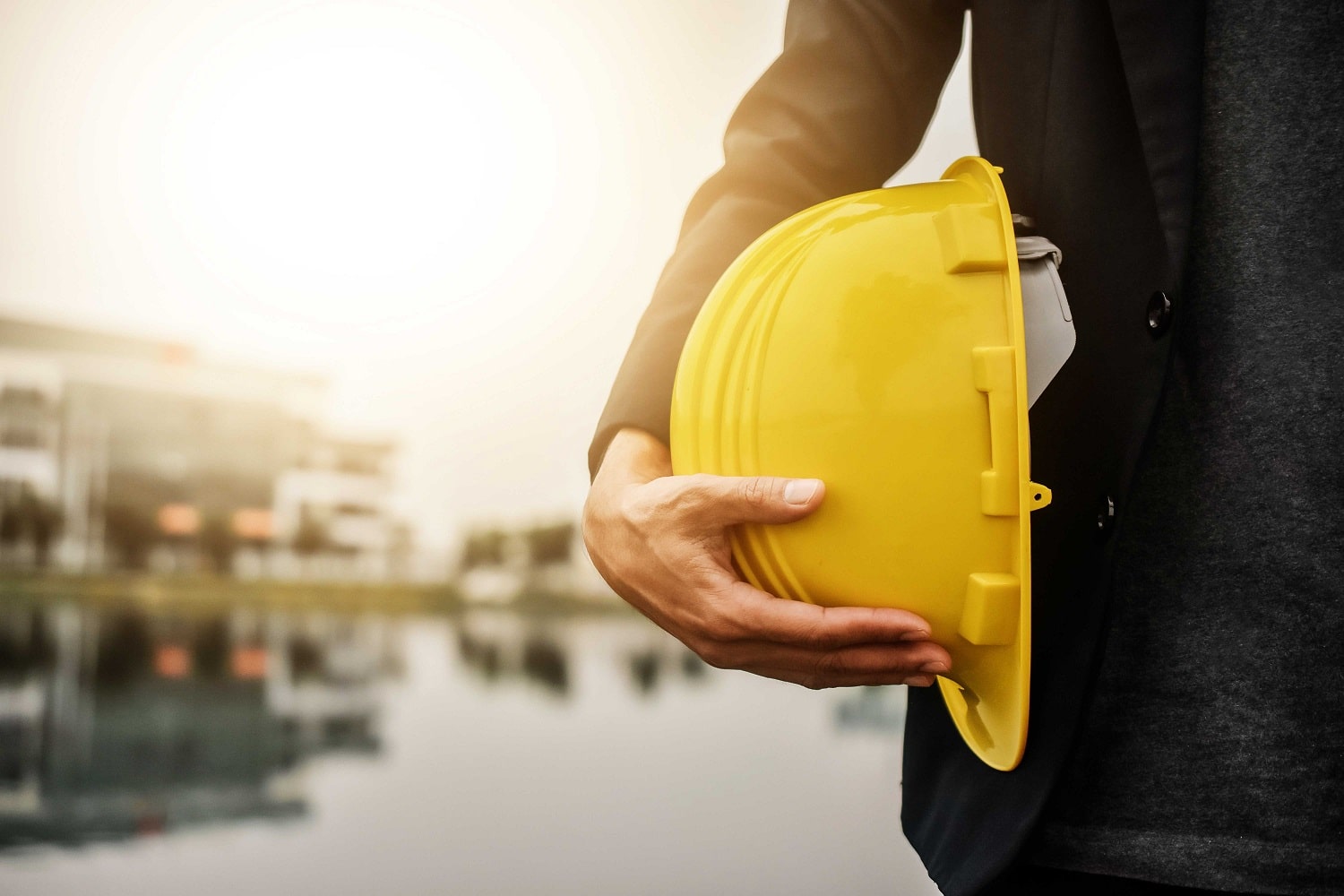