At a glance:
– Introduction
– What is MRO?
– Examples of MRO inventory
– Why is MRO necessary?
– How does MRO affect supply chain management?
– What are the best MRO practices for supply chain management?
– Conclusion
– About VisiumKMS
A successful production process is the backbone of any business and plays a pivotal role in ensuring that the business runs profitably. Various factors are involved in ensuring a robust and cost-effective production process and one such important factor is MRO i.e. maintenance, repairs and operations. Read this blog to learn what exactly is MRO, its importance and how MRO affects supply chain management.
To begin with, what is MRO?
In simple words, MRO stands for maintenance, repair, and operations and refers to a set of operations and activities that are associated with the upkeep of a plant or facility which can include the physical maintenance of the structure or building, the systems that operate within the facility, and the equipment used to produce the plant or facility’s primary business output. MRO’s main goal is to ensure streamlined operations and the overall smooth functioning of the business.
Next, let’s have a look at what falls under maintenance, repair, and operations. Some examples of MRO inventory include –
- Facility Management:
The facility could be anything- your factory, your office, your warehouse, or storage space. Facilities make for an important part of the company since this is where the entire production process happens, and they thus are a vital tool in MRO. It is important to ensure that everything in the building is periodically serviced and maintained. All the materials involved in this process fall under facility management. - Industrial Equipment:
This refers to items and pieces of equipment that are necessary for a business to function smoothly, be it in the manufacturing process of a product or for offering a service like shipping. It includes different types of materials used for machines and equipment such as motors, pumps, machine oil, lubricants, nearing, cutting fluid, spare parts, and valves. It also includes the maintenance and repair supplies necessary for production machinery as they also play a critical role in running the business smoothly. Laboratory supplies for testing and research which includes breakers, syringe, and test tubes also form an integral part of the MRO. - Safety Tools:
MRO inventory with respect to safety tools involves masks, ear plugs, hard hats, respirators, and face shields. Malfunctioning equipment or a hazardous working environment not only delays the production process but can also prove to be fatal to those working around it. This is why safety equipment must not be overlooked in maintenance, repair, and operations at any cost.
To learn how ESG reporting can benefit your business, read this.
- Consumables:
Lastly, consumables include cleaning, office or maintenance, repair, and operation supplies which could be pens, paper, pencils, cleaning sprays, mops, buckets, brooms, etc. These things are also just as important to a business, to ensure its smooth functioning on a day-to-day basis.Now that we have understood what is MRO, let’s understand why is MRO necessary –
It is important to ensure that you have a balanced quantity of MRO inventory available with you, in order to keep the business running. Running low on a certain product or essential equipment can snowball into hours and weeks of downtime which will lead to the business losing revenue. Stockpiling on MRO inventory on the other hand can lead to money being invested somewhere other than the focus of the business. Furthermore, since the possibility of an item getting obsolete is high, is all the more reason why maintaining a balanced MRO inventory is essential.
Improperly managed MRO items can have a disastrous impact on the supply chain. Some of the key benefits of prioritizing MRO for the business are mentioned below –
- Enhanced Workflow:
If a machine is malfunctioning or a piece of equipment has broken down due to wear and tear, it might lead to disruption in the business workflow. With proper MRO management, detecting and fixing wear and tear becomes easy, which prevents bigger problems like downtime and makes sure that the production process is running smoothly. - Cost-effectiveness:
You might see maintenance, repair, and operations as an added cost, but in reality, they are saving you money in the long run. With machines, equipment, tools, and components periodically serviced and maintained, the chances of disruption in workflow get reduced, thus downtime is minimized. Furthermore, MRO can help predict and prevent any unexpected repair and maintenance early on. Moreover, since the maintenance, audits, repairs, and appointments are scheduled for a particular time, less time will be wasted in dealing with unexpected repairs. MRO planning thus saves a significant amount of money for a business in the long run. - Safety:
Last but not least, by periodically servicing, maintaining, and repairing the facility and the equipment in the facility, you can ensure that the plant, factory, or warehouse becomes safer for the workers to work in. Preventing maintenance in MRO can help uncover flaws and faults which can be fixed at the right time, thereby avoiding the possibility of any accidents in the future.
To gain a detailed understanding of OSHA’s process safety management regulation, read this.
How does MRO affect supply chain management?
MRO inventory management includes buying, storing, utilizing, and replenishing all the different tools and components that are included in MRO. Managing MRO inventory can be a taxing process but it is important to ensure that it is done in an efficient and economical manner. Since it doesn’t directly contribute to the final product, how MRO affects supply chain management is often overlooked. The adequate allocation of maintenance and repair can make or break the supply chain and having proper MRO in place can impact the overall safety, profitability, and longevity of the business.
How MRO affects supply chain management depends entirely upon the practices that are put in place to avoid over or under-stocking of the materials, tools, and equipment. If the tools and equipment are not maintained and repaired on time, it can increase the risk of untimely equipment malfunction. This will not only lead to increased downtime but result in extra costs associated with fixing the damage due to malfunctioning pieces.
When an MRO stock management is unoptimized, it can increase the possibility of MRO stockout which directly impacts and causes downtime and unnecessary MRO spending. Furthermore, poor MRO practices like inefficient order policies or approaching the budget with a product pricing mindset instead of the total cost of ownership can increase the cost associated with MRO and the freight expenses.
Proper MRO inventory management practices can help you ensure that you are keeping an eye on the MRO inventory and stocks thus making sure that you never run out of supplies. This will also make certain that the shortage gets noticed in due time and that proper action can be taken to replenish the products.
Optimized MRO management will also ensure that your business is saving money in the long run. You can save money on transportation and shipping by making the right decision ahead of time which will help uncover deals on spare parts and raw materials. On the other hand, if you wait till the last minute for the inventory to get exhausted you might end up paying a large sum for the materials as well as delivery.
What are the best MRO practices for supply chain management?
Now that we have discussed how does MRO affect supply chain management, let us look at some of the best practices that can prove to be instrumental in making supply chain management more efficient:
- Educate the Staff:
By offering educational plans like seminars to your employees, you can help them understand the importance of following the MRO practices. Some of the areas where you can educate your staff is:
– Establishing where the inventory exists and understanding the system that keeps track of the inventory
– Help them understand the functioning of your order management system in detail
– How to update the existing order management system and track inventory in real-time
- Establish Shipping Metrics:
This will help in auditing and measuring certain factors associated with MRO like savings, overheads and obsolescence. The shipping metrics can be the number of stockouts, in-hand inventory, rates of parts obsolescence, unaccounted spend to the procurement budget, MRO spend as a percentage of the procurement budget, and more.
- Centralize MRO inventory:
Improve the visibility of MRO inventory by storing them in a centralized and trackable location. This will help you increase or decrease the inventory size as per the supply chain performance standards at the right time.
In conclusion, the need for a supply chain will evolve as the business evolves. This is why it is important to have proper MRO strategies in place to ensure that the supply chain is efficiently managed at all times. The right MRO practice will help you combat unplanned downtime and maximize the return which will boost your supply chain’s sustainability.
About VisiumKMS:
VisiumKMS provides a comprehensive suite of tools for planning and executing audits, and managing the actions from findings and lessons learned. It involves –
- Managing the entire audit lifecycle, including protocol development, audit planning, audit execution, and managing post-audit actions.
- Providing intuitive protocol administration features for any protocol, external or internal, and simplifying the execution of ad hoc audits; also managing the closure of the post-audit recommendations.
- Ensuring permissions-based access to workflows and information pertaining to internal and external auditors.
At VisiumKMS, we commit to staying ahead of the curve; to help our customers keep ahead of the business and operational pressures, regulations, and global or local challenges they face. To discuss your needs with one of our experts, schedule a call with us here.
Listed here are 5 reasons stating the importance of chemical inventory management.
–
Effective chemical inventory management is an absolute must for any organization that uses chemicals as a part of its day-to-day operations. Not only is it a mandatory requirement by OSHA but also an essential component for hazard management. This blog elucidates the importance of chemical inventory management.
To begin with, let’s understand what exactly is chemical inventory management?
Simply put, chemical inventory management is the process of organizing and tracking chemicals at all stages – right from their procurement, storage and usage to disposal.
So why is it so important?
Listed below are 5 reasons stating the importance of chemical inventory management –
- Safety At Workplace:
First and foremost, it plays a significant role in ensuring safety at workplace. Some of the chemicals can be highly hazardous or toxic in nature and if handled inattentively, can lead to accidents, explosions, health complications or some serious injuries at work. Meticulous chemical inventory management enables organizations to take active steps to minimize such risks to a great extent. - Legal Compliance:
Next, practising thorough chemical inventory management is also a mandatory requirement under certain regulations. For example, OSHA’s Hazard Communication Standard (HCS) requires organizations that use hazardous chemicals to evaluate the hazards of the chemicals they produce or import, and prepare labels and safety data sheets to convey the hazard information to their downstream customers. In addition to that, it asks them to train their employees for appropriate handling and usage of these chemicals. - Cost-Effectiveness:
As mentioned earlier, chemical inventory management involves maintaining records and tracking inventory at regular intervals. By analyzing this data, one can understand their exact inventory requirement and make informed decisions for procurement of chemicals in the future. In essence, it facilitates organizations to operate efficiently by avoiding ordering in excess which can lead to a potential loss to the business. - Promotes Sustainability:
Thereafter, as a result of optimum utilization of resources, it helps in reducing wastage thereby promoting sustainability! In current times, consumers and investors alike take into account a company’s commitment to sustainability before associating with it. Hence, as an added advantage, it helps organizations nurture their relationship with their stakeholders and gain a competitive advantage.To learn about the top 4 benefits of carbon management, click here.
- Emergency Response:
Last but not the least, it is a key component of an emergency response plan (ERP). An emergency reponse plan is a set of written procedures for dealing with emergencies that prioritizes life safety, minimizes the impact of the event and facilitates recovery from the event. Since chemical inventory management involves maintaining complete information regarding the hazardous chemicals like their properties, quantity in stock and where they are located, it proves to be of great help while taking crucial decisions during an emergency.
At VisiumKMS, we are committed to staying ahead of the curve. Our process safety management software helps companies maintain all their process safety information in one system, using best-in-class, standardized workflows developed by industry experts! To discuss your needs with one of our experts, schedule a call with us here.
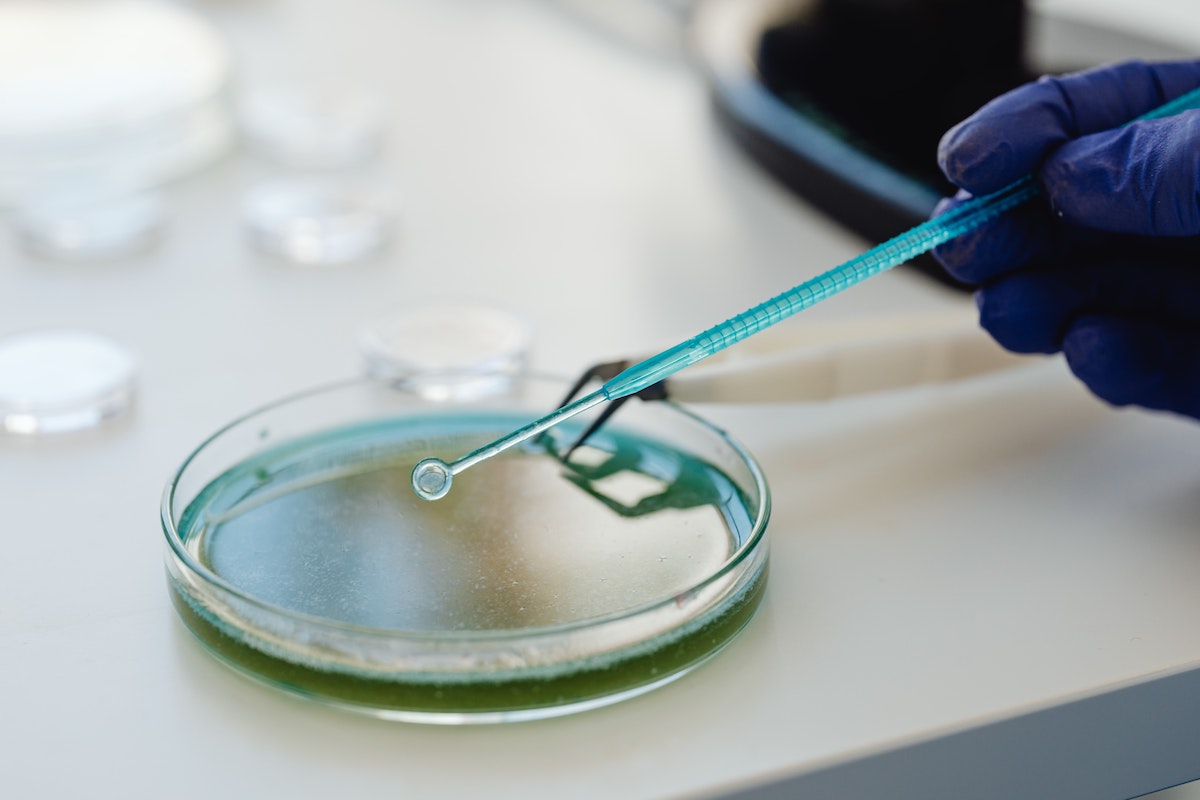